-
- Tổng tiền thanh toán:
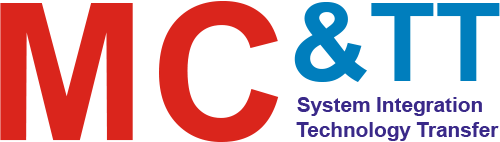
Giới thiệu giải pháp, sản phẩm, ứng dụng bộ lập trình nhúng PAC, Bo mạch, Card EtherCAT Master hãng ICP DAS
EtherCAT (Ethernet Control Automation Technology) is a series of Ethernet-based industrial communication buses. It has established the mainstream in the industrial automation industry pursuing high precision, high efficiency, and low cost due to its high-speed communication performance and instant communication system.
Features
EtherCAT (Ethernet Control Automation Technology) is a series of Ethernet-based industrial communication buses. It has established the mainstream in the industrial automation industry pursuing high precision, high efficiency, and low cost due to its high-speed communication performance and instant communication system.
EtherCAT is industrial Ethernet
The optimized EtherCAT data is included in the IEEE 802.3 Ethernet frame. The frame travels through the media at 100 Mbps in full-duplex mode.
Flexible Topologies
With two EtherCAT ports on all devices, no additional switches are required to create a linear network. EtherCAT junction slaves can be used to build tree and star topologies.
Distributed Clocks
The EtherCAT node slave measures the time difference between incoming and returning frame - timestamp-. With these
timestamps the master can determine the propagation delay offset to the individual slave accurately. This mechanism ensures accurate synchronization between devices with less than 1 μs jitter.
Simple cabling
100Base-TX EtherCAT uses standard 100BASE-TX Ethernet
communication very effi ciently, over standard shielded Ethernet cables and connectors. No need for network switches.
Easy use, easy connect
When compared to a classic fieldbus system, EtherCAT is the obvious choice: node addresses can be set automatically, there’s no need for network tuning, and onboard diagnostics with fault localization make
pinpointing errors a snap. Despite these advanced features, EtherCAT is also easier to use than Industrial Ethernet: there are no switches to configure, and no complicated handling of MAC or IP addresses is required.
Processing on the fly
The slave devices extract and/or insert data on the fly. This method assures the highest possible throughput.
Applications of Motion Control
Access to Parts and Component
- Transfer and stacking device
- Gantry pick and place
- Pick, place, measure, and sort components automatically
Conveying Syste
- Positioning of the workpiece on the conveyor
- Handling and transportation equipment
- Product inspection
- Online Pallet Stacker
- Labeling machine
Parts Assembly Syste
- Precision spot welding machine
- Sealing, gluing, joining applications
- Add glue on the surface to connect parts
- Sealing: apply sealant on the joint surface of the parts
- Dispenser: gluing.
Warehousin
- Automated storage and retrieval system
- Automatically store and retrieve pallets from the storage cabinet
Applications of Cutting, Grinding and Pressing
Semiconductor Manufacturin
- IC inspection
- IC chip installation and assembly
- Pick up components and place them on the printed circuit board
- Camera Detection:
- Check with a mobile camera.
- Use the camera to conduct multi-point inspections
Robot Contro
- Control single axis robot
- Control multiple single-axis robots for spraying applications
- Dual drives: synchronize and move two single-axis robots of the same type
List of Common Drivers and Motors That Have Been Market Tested
Company | Drivers | Types of Motors |
---|---|---|
Delta | ASDA A2-E series | AC Servo Motor |
Hiwin | D2 series | AC Servo Motor |
Moons' | STF/RS series | Two-phase Stepper Motor |
Mitsubishi | MR-JET | AC Servo Motor |
Oriental Motor | AZ series multi-axis | Closed loop Stepper Motor |
Panasonic | A5B/A6B series | AC Servo Motor |
Shihlin | SDP series | AC Servo Motor |
Sanyo Denki | R series | AC Servo Motor |
Teco | JSDG2/JSDG2S | AC Servo Motor |
Yaskawa | Sigma 7 series | AC Servo Motor |
Bộ lập trình nhúng PAC Master
EtherCAT Master based 9000 series PAC |
||||||||
Model | ||||||||
---|---|---|---|---|---|---|---|---|
CPU | RAM | I/O Slot | Cycle Time | EtherCAT Slaves | EtherCAT Axes | |||
EMP-9051-16
|
i5-8365UE | 16 GB | 0 | .5/1/2/4/8 ms | Max. 512 | Max. 16 | ||
EMP-9051-32
|
Max. 32 | |||||||
EMP-9251-16
|
2 | Max. 16 | ||||||
EMP-9251-32
|
Max. 32 | |||||||
EMP-9651-16
|
6 | Max. 16 | ||||||
EMP-9651-32
|
Max. 32 | |||||||
EMP-9091-16
|
Atom E3950 | 8 GB | 0 | Max. 16 | ||||
EMP-9091-32
|
Max. 32 |
SoftPLC Based EMP-9000 Motion Controller Series |
||||||||
Model | ||||||||
---|---|---|---|---|---|---|---|---|
CPU | RAM | I/O Slot | Cycle Time | EtherCAT Slaves | EtherCAT Axes | |||
EMP-9058-16
|
i5-8365UE | 16 GB | 0 | 0.5 ms (min) | Max. 512 | Max. 16 | ||
EMP-9058-32
|
Max. 32 | |||||||
EMP-9258-16
|
i5-8365UE | 16 GB | 2 | Max. 16 | ||||
EMP-9258-32
|
Max. 32 | |||||||
EMP-9098-16
|
Atom E3950 | 8 GB | 0 | Max. 16 | ||||
EMP-9098-32
|
Max. 32 |
Compact EtherCAT Master PAC |
|||||||
Model | |||||||
---|---|---|---|---|---|---|---|
OS | CPU | System Memory | Storage | EtherCAT | |||
Cycle Time | Number of Slaves | Number of Axes | |||||
EMP-2848M
|
Real-Time Linux (RT-Preempt) | Cortex-A53, Quad-core, 1.6GHz | LPDDR4 - 1GB | eMMC Flash – 8GB, 4GB microSD card | 500 μs (min.) | 128 | 16 |
Card, Bo mạch, PC Board EtherCAT Master
Master Series |
||||||||
Model | EtherCAT | Encoder Input | Digital Input & Output | Accessories | ||||
---|---|---|---|---|---|---|---|---|
Port | Axes | Slave | Response Speed | Resolution | Channels | Daughter Board | Cable | |
ECAT-M801-8AX
|
1 x RJ-45 | Max. 8 | Max. 64 | 1 MHz | 32-bit | 13-ch DI & 13-ch DO | - | - |
ECAT-M801-16AX
|
Max. 16 | |||||||
ECAT-M801-32AX
|
Max. 32 | |||||||
ECAT-M801-64AX
|
Max. 64 | |||||||
ECAT-M801-8AX/S
|
1 x RJ-45 | Max. 8 | Max. 64 | 1 MHz | 32-bit | 13-ch DI & 13-ch DO | Yes | Yes |
ECAT-M801-16AX/S
|
Max. 16 | |||||||
ECAT-M801-32AX/S
|
Max. 32 | |||||||
ECAT-M801-64AX/S
|
Max. 64 |