-
- Tổng tiền thanh toán:
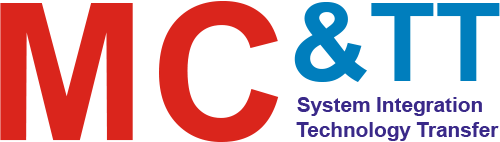
Giới thiệu giải pháp, sản phẩm, ứng dụng truyền thông CANopen hãng ICP DAS
CANopen is a CAN-based application layer protocol. It was developed as a standardized embedded network with highly flexible configuration capabilities. CANopen was designed for motion-oriented machine control networks, such as handling systems. By now it is used in many various fields, such as medical equipment, off-road vehicles, maritime electronics, public transportation, building automation, etc.
The CANopen specifications cover application layer and communication profile, as well as a framework for programmable devices, recommendations for cables, connectors, SI units, and prefix representations. The application-layer as well as the CAN-based profiles are implemented in software.
CANopen features
- Allow multi-master architecture on one bus
- 10k,20k,50k,125k,250k,500k,800k,1M bps baud rate
- The bus length is from 25m(1M bps) to 5Km(10K bps)
- Easy access to all device parameters.
- Device synchronization.
- Cyclic and event-driven data transfer.
- Up to 128 nodes can be participated in the same CAN network.
- High transmission speed.
- Support Guarding and Heartbeat protection mechanism
CANopen Communication
INITIALISING | PRE-OPERATIONAL | OPERATIONAL | STOPPED | |
---|---|---|---|---|
PDO | X | |||
SDO | X | X | ||
Synchronisation object | X | X | ||
Time Stamp Object | X | X | ||
Emergency Object | X | X | ||
Boot-Up Object | X | |||
Network Management Object | X | X | X |
CANopen Statue Transition
Lifhtweight Device Monitoring
CANopen provides two network protection mechanisms, Node Guarding and Heartbeat. For Node Guarding, the master will send a request to check slave status. If some slave does not confirm this request, the master will indicate them with Node Guarding Fail. For Heartbeat, these slaves will send heartbeat message to the master let master know these slaves are alive. If the master does not detect some one’s heartbeat, then the master will indicate it with Heartbeat Fail.
CANopen Digital I/O Pair-connection
CANopen Digital I/O Pair-connection is a special function for CANopen remote I/O. It can send the DI value that is detecting by the CANopen DI Slave to others CANopen DO Slaves through the CANopen network, and then these CANopen DO Slaves will output the value. It is useful for users need to detect a DI signal and output a DO alarm at the same time.
Remote I/O Module and Unit
CAN-2000 series and CAN-8000 series are designed for combining sensors and actuators into, CANopen or DeviceNet network. All of them provide corresponding EDS files for standard CANopen or DeviceNet master interfaces. The mainly differences between CAN-2000 series and CAN-8000 series are the product size and the capabilities of I/O expansion. CAN-2000 series is a palm-size and stand-along slave device. CAN-8000 series is useful for centralizing control system. It provides 1/2/4/8 slots for fl exible I/O selections to match various applications. Each slot allows you plugging one I-8000/I-87K series I/O module to expand I/O channels, and hot-swap technique is supported.
With the same hardware, the CAN-2000 series and CAN-8000 series can be installed either of, CANopen fi rmware. The product names are classifi ed as
CANopen: CAN-8x23, CAN-2xxxC
CANopen Series Common Features
- Up to 128 nodes can be participated in the same CAN network
- CANopen Version: DS-301 v4.01
- Device Profile: DSP-401 v2.0
- Error Control: Node Guarding protocol
- Emergency Message: Yes
- 2500Vrms photo couple isolation on the CAN side
- Jumper or DIP switch for 120Ω terminal resistor of CAN bus
- Watchdog inside
Multifunction I/O Module |
||||||||
Model | Analog Input | Analog Output | Digital Input | Digital Output | ||||
---|---|---|---|---|---|---|---|---|
Channels | Input Range | Channels | Output Range | Channels | Contact | Channels | Type | |
CAN-2026C | 6 | ±10 V, ±5 V, ±1 V, ±500 mV, ±150 mV, ±20 mA (with external 125 Ω resistor) |
2 | 0 ~ +5 V, ±5 V, 0 ~ +10 V, ±10 V |
2 |
Wet, Sink |
1 | Open Collector, CAN-2026D DeviceNet Sink |
CAN-2022C | 2 | ±10V, ±5V, ±2.5V, ±1.25V, ±1V, ±500mV, ±250mV | 2 | 0 ~+5V, +/-5V, 0~+10V,+/-10V |
4 | Wet contact (Sink) | 4 | Isolated Open Collector (Sink) |
Analog I/O Modules |
|||||
Model | Analog Input | Analog output | |||
---|---|---|---|---|---|
Channels | Input Range | Sensor | Channels | Output Range | |
CAN-2015C | 8 | - | RTD (Pt100, Pt1000, Ni120, Cu100, Cu1000, Pt100) | - | - |
CAN-2017C | 8 | ±10 V, ±5 V, ±1 V, ±500 mV, ±150 mV, ±20 mA (with external 125 Ω resistor) |
- | - | - |
CAN-2018C/S | 8 | ±2.5 V, ±1 V, ±500 mV, ±100 mV, ±50 mV, ±15 mV, ±20 mA (with external 125 Ω resistor) |
Thermocouple (J, K, T, E. R. S, B, N, C) |
- |
- |
CAN-2019C/S | 10 | ±10 V, ±5 V, ±2.5 V, ±2 V, ±500 mV, ±100 mV, ±50 mV, ±15 mV, ±20 mA (with external 125 Ω resistor) |
Thermocouple (J, K, T, E. R. S, B, N, C) |
- | - |
CAN-2019C/S2 | |||||
CAN-2024C | - | - | - | 4 | 0 ~ +5 V, ±5 V, 0 ~ +10 V, ±10 V, 0 ~ 20 mA, 4 ~ 20 mA |
Digital I/O Modules |
||||||
Model | Digital Input | Digital output | ||||
---|---|---|---|---|---|---|
Channels | Contact | Sink/Source | Channels | Type | Sink/Source | |
CAN-2053C | 16 | wet | Sink/Source | - | - | - |
CAN-2054C | 8 | wet | Sink/Source | 8 | Open Collector | Sink |
CAN-2055C | 8 | wet | Sink/Source | 8 | Open Source | Source |
CAN-2057C | - | - | - | 16 | Open Collector | Sink |
CAN-2060C | 4 | wet/Dry | Sink/Source | 4 | Relay | Form A, 5A |
Counter/PWM Modules |
||||||||
Model | Counter Input | PWM Output | ||||||
---|---|---|---|---|---|---|---|---|
Channels | Signal | Resolution | Speed | Channels | Load Current | Resolution | Speed | |
CAN-2084C | 4 / 8 | Up, Up/Down, Dir/Pulse, A/B phase, Frequency | 32 bit | 250 kHz | - | - | - | - |
CAN-2088C | 8 | Up Counter | 32 bit | 500 kHz | 8 | 1 mA | 16 bit | 500 kHz |
Remote I/O Unit |
|
Model | Product Description |
---|---|
CAN-8123-G | CANopen Embedded Device with 1 I/O Expansion Slot, support I-87K module and I-8K module |
CAN-8223-G | CANopen Embedded Device with 2 I/O Expansion Slots, support I-87K module and I-8K module |
CAN-8423-G | CANopen Embedded Device with 4 I/O Expansion Slots, support I-87K module and I-8K module |
CAN-8823-G | CANopen Embedded Device with 8 I/O Expansion Slots, support I-87K module and I-8K module |
Modules Support
Type | I-8K Series I/O | I-87K Series I/O | Type | I-8K Series I/O | I-87K Series I/O | ||||
---|---|---|---|---|---|---|---|---|---|
High Profile | Low Profile | High Profile | Low Profile | High Profile | Low Profile | High Profile | Low Profile | ||
AI module | I-8014W | DI module | I-8026W | ||||||
I-8014CW | I-8017H | I-87005W | I-8040W | I-8040 | I-87040W | I-87040 | |||
I-8017HS | I-87013W | I-87013 | I-8040PW | I-87040PW | |||||
I-8017HW | I-8040W-A1 | ||||||||
I-8017DW | I-87015W | I-8046W | I-87046W | ||||||
I-8017HCW | I-87015PW | I-8048W | I-8048 | I-87051W | I-87051 | ||||
I-8026W | I-87016W | I-8051W | I-8051 | I-87052W | I-87052 | ||||
I-87017W | I-87017 | I-8052W | I-8052 | I-87053W | I-87053 | ||||
I-87017W-A5 | I-8053W | I-8053 | I-87053PW | ||||||
I-87017W-RMS | I-8053PW | I-87053W-A5 | |||||||
I-87017RCW | I-8053W-A1 | I-87053W-A2 | |||||||
I-87017DW | I-8058W | I-8058 | I-87053W-AC1 | ||||||
I-87017ZW | I-87053W-E5 | ||||||||
I-87017RW | I-87058W | I-87058 | |||||||
I-87059W | |||||||||
I-87018W | I-87018 | ||||||||
I-87018PW | AO module | I-8024W | I-8024 | I-87024RW | I-87022 | ||||
I-87018RW | I-8024UW | I-87024W | I-87024 | ||||||
I-87018ZW | I-8028UW | I-87024DW | I-87026 | ||||||
I-87019RW | I-8026W | I-87024UW | |||||||
I-87019PW | I-87028UW | ||||||||
I-87019ZW | I-87028VW | ||||||||
DO module | I-8026W | ||||||||
I-8037W | I-8037 | I-87037W | I-87028VW-20V | ||||||
I-8041W | I-8041 | I-87041W | I-87041 | I-87028CDW | |||||
I-8041PW | I-87041PW | ||||||||
I-8041AW | I-87057W | I-87057 | |||||||
I-87057PW | DI & DO module | I-8042W | I-8042 | I-87054W | I-87054 | ||||
I-8056W | I-8056 | I-87061W | |||||||
I-87061PW | I-8050W | I-8050 | I-87055W | I-87055 | |||||
I-8057W | I-8057 | I-87064W | I-87064 | ||||||
I-8057PW | I-8054W | I-8054 | I-87063W | I-87063 | |||||
I-8060W | I-8060 | I-87065W | I-87065 | I-8055W | I-8055 | ||||
I-8064W | I-8064 | I-87066W | I-87066 | I-8063W | I-8063 | ||||
I-8065 | I-87068W | I-87068 | |||||||
I-87068W-2A | I-8077 | ||||||||
I-8066 | I-87069W | I-87069 | |||||||
I-8068W | I-8068 | I-87069PW | Counter module | I-8084W | I-8080 | ||||
I-8069W | I-8069 | PWM module | I-8088W |
Gateway
The Modbus TCP/RTU and DCON protocol gateways are ready for users. The series can be used to integrate different protocol system. Users also easily update their old system to the CANopen system with the series. They are I-7231D, I-7232D, GW-7433D.
Model | CANopen Gateway | ||
---|---|---|---|
Module Name | I-7231D-G | I-7232D-G | GW-7433D |
Product Description | CANopen Slave to DCON Master Gateway | CANopen Slave to Modbus RTU Master Gateway | Modbus TCP/RTU Slave to CANopen Master Gateway |
CANopen Interface | |||
CANopen Interface | 1 channel (CAN_H, CAN_L), and the other is for bypass | ||
CANopen Function | CANopen slave | CANopen master (Supports at least 120 CANopen commands) |
|
CANopen Baud Rate | 10 k, 20 k, 50 k, 125 k , 250 kbps , 500 k, 800 k, 1M | ||
CANopen Version | CiA 301 v 4.02 and CiA 401 v2.01 | ||
Guarding Function | Yes | ||
Heartbeat Function | Heartbeat Producer | Heartbeat Consumer | |
Emergency Message | Yes | - | |
UART Interface | |||
COM1 Connector | RS-232 (TxD, RxD, RTS, CTS, GND) or RS-485 (Data+, Data-), Non-isolated | RS-232 (TxD, RxD, RTS, CTS, GND), Non-isolated | |
COM1 Function | Only for configuration | Modbus RTU Slave | |
COM2 Connector | RS-485 (Data+, Data-) with internal Self-Tuner ASIC; Non-isolated | ||
COM2 Function | DCON Master (Supports Max. 15 I-7K or I-87K modules) |
Modbus RTU Master (Supports Max. 10 Modbus RTU ommands) |
Modbus RTU Slave |
Ethernet Interface | |||
Ethernet | - | 10/100 Base-TX | |
Ethernet Function | - | Configuration or Modbus TCP Server | |
Modbus Function Code | - | 01, 02, 03, 04, 06, 15 | 01, 02, 03, 04, 05, 06, 15,16 |
Comunication Module
CANopen Master Selection Guide |
|
Model | Product Description |
---|---|
PISO-CPM100-D | 1 Port Intelligent CANopen Master PCI Board |
PISO-CPM100-T | 1 Port Intelligent CANopen Master PCI Board |
PISO-CPM100U-D | 1 Port Intelligent CANopen Master Universal PCI Board |
PISO-CPM100U-T | 1 Port Intelligent CANopen Master Universal PCI Board |
PCM-CPM100-D | 1 Port Isolated Protection CAN Communication PCI-104 Module |
I-8123W-G | 1 Port High Performance Intelligent CANopen Master Module |
I-8123W-CPS-G | 1 Port high performance CANopen Slave Module |
I-87123-G | 1 Port Intelligent CANopen Master Module |
I-7565-CPM-G | USB to CANopen Master Converter |
CANopen Master Series:
Product Name | I-7565-CPM | PISO-CPM100(U) | PISO-CAN 200/400(U) | PEX-CAN200i | I-8123W | I-87123 |
---|---|---|---|---|---|---|
Hardware | ||||||
On board CPU | 16-bit CPU 80M Hz |
16-bit CPU 80M Hz |
None | None | 16-bit CPU 80M Hz |
16-bit CPU 80M Hz |
Interface | USB | 5 V / 3.3 V PCI bus | 5 V / 3.3 V PCI bus |
x1 PCI Express bus | I-8K Slot (WinPAC,XPAC) | I-87K Slot (WinPAC,ViewPAC) |
CAN Connector | 9-pin D-Sub | 5-pin screw terminal 9-pin D-Sub |
5-pin screw terminal 9-pin D-Sub |
5-pin screw terminal 9-pin D-Sub |
5-pin screw terminal | 5-pin screw terminal |
CAN Controller | SJA1000 | |||||
CAN Transceiver | 82C250 | |||||
Isolation on CAN | 2500 Vrms | |||||
Terminal Resistor | Selected by jumper(120Ω) | |||||
CANopen | ||||||
Protocol Specification | CANopen Standard -- CiA Draft Standard 301 | |||||
Baud Rate Selection | Programmable | |||||
Baud Rate | 10 kbps, 20 kbps, 50 kbps, 125 kbps , 250 kbps , 500 kbps, 800 kbps, 1000 kbps | |||||
Maximum Slave nodes | 127 Nodes | |||||
PDO Function | Support dynamic PDO function | |||||
PDO Object | Provide 20 RxPDO and 20 TxPDO object | |||||
EMCY Message | Save the least EMCY | |||||
SDO Protocol | Support Expedited SDO and Segment SDO protocol | |||||
On Line Edit Nodes | Support adding or removing devices on line | |||||
NMTError Control | Support Node Guarding Event | |||||
Driver | ||||||
DLL | Support | |||||
OS Version | Win 2K/XP | Windows XP/7/8/10 (32-bit/64-bit OS) | Win CE 6/7, WES7 | Win CE 5/6 | ||
Development Tool | Visual C++ 6 , Visual Basic 6 , Borland C++ Builder , Delphi | VS .NET | eVC++ 4 , VS .NET |
Comparison with PISO-CPM100 and PISO-CAN 200/400-D/T
Hardware Compare
Performance Test with PISO-CPM100 and PISO-CAN 200/400-D/T
Product Name | PISO-CPM100 | PISO-CAN-200/400 with CANopen Library |
---|---|---|
Protocol decoder | 186 CPU | PC CPU |
Time stamp | 186 Timer (0.1 ms) | PC Timer (about 1 ms) |
CPU Loading | Light | Heavy |
Performance | High | Normal |
Application | Various and complex CANopen application | General purpose CANopen application |
Test environment:
CPU:Intel(R) Pentium(R) 4 CPU 2.40 GHz
OS:Microsoft Windows XP Professional Version 2002 Service Pack 2
RAM:512 MB
CAN Baudrate:1000 bps
Test result:
Function | PISO-CPM100 (ms) | PISO-CAN200/400 with CANopen library (ms) |
---|---|---|
Add Node | Average 45.502 | 1265 ~ 1280 |
Read 4 bytes data by SDO | Average 2.487 | 19.37 ~ 19.47 |
Read 9 bytes data by SDO | Average 2.971 | 58.21 ~ 58.61 |
Write 4 bytes data by SDO | Average 2.479 | 18.81 ~ 19.69 |
Read 8 bytes data by PDO | Average 2.355 | 16.49 ~ 16.57 |
Write 8 bytes data by PDO | Average 1.738 | 0.13 |
Note 1:
The data of above list is average of 1000 message.
Node 2:
If user use the guarding function with PISO-CAN200/400 with CANopen library, the guard error event may be occured when the slave is more and the guarding time is shorter. This is because of that the accuracy of timer of windows is not enough.
Motion Library (CiA 402)
The I-8123W/PISO-CPM100U provides the motion control library now. This library follows the CANopen standard CiA 402. It is available on the ViewPAC / WinPAC / XPAC platform. The CiA 402 is one kind of the standard CANopen application profiles, and specially designed for motion control systems. In addition to making the management of the CANopen motors easy, this communication protocol can reduce the wire connection between the controller and motors, and provide rapid troubleshooting functions. With the I-8123W/PISO-CPM100U and CANopen Motion Library, you can do various motion control functions, such as position control, velocity control, toque control, and synchronous action without having the background knowledge of the complex and abstruse CANopen protocol. The CANopen Motion Library is able to link many CANopen motors so that the multi-axis motion control by one host becomes reachable. While controlling motors, you can also use the APIs of the I-8123W/PISO-CPM100U library to access CANopen remote I/O modules which follows the CiA 401 at the same time. Therefore, building a motion control application becomes more easy and convenient.
Feature:
- Compliant with CiA 402 v1.1
- Reduce 50% wires connection cost
- Physical layer with fault tolerance and anti-noise
- Support max. 127 motors in one network
- Absolute and relative position control
- Velocity control
- Torque control
- JOG control
- Support max. 127 motors synchronous action
- Various Homing control
- Support torque limitation with CANopen command
- Support Win 2000/XP/Vista or Win 7(32-bit version)